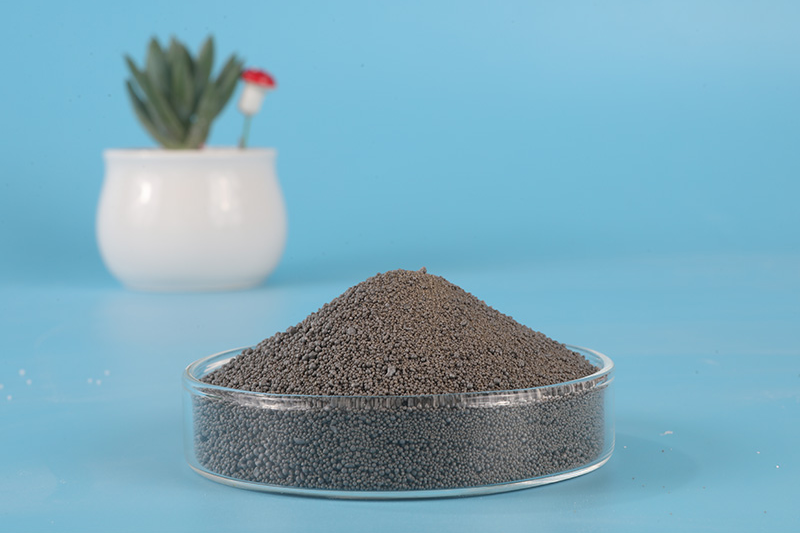
Wood Plastic Composite Material - Application of Polymer Special Lubricant
Wood plastic composite (WPC) materials have gained significant attention in recent years as a sustainable alternative to traditional wood products. WPC combines the advantages of wood fibers or particles with polymer matrices to create a versatile material with diverse applications. One critical aspect of optimizing the performance of WPC is the effective incorporation of lubricants. This article explores the application of polymer special lubricants in WPC materials, highlighting their role in enhancing processability, improving mechanical properties, and promoting overall product quality.
Processability Enhancement:
Polymer special lubricants play a crucial role in improving the processability of WPC materials during extrusion and injection molding. By reducing friction between the wood fibers and the polymer matrix, lubricants facilitate the smooth flow of the composite during processing. This leads to enhanced throughput rates, reduced energy consumption, and improved dimensional stability of the final product. The use of lubricants also minimizes equipment wear, resulting in extended tool life and reduced maintenance costs.
Mechanical Property Improvement:
Incorporating polymer special lubricants in WPC formulations can significantly enhance the mechanical properties of the resulting composite materials. The lubricants help to reduce the interfacial friction between the wood fibers and the polymer, thereby improving the dispersion of the wood particles within the matrix. This improved dispersion leads to enhanced bonding between the wood and polymer phases, resulting in increased tensile strength, flexural strength, and impact resistance of the WPC material. Furthermore, lubricants aid in reducing moisture absorption by the wood fibers, thus improving dimensional stability and resistance to warping or cracking.
Surface Quality Enhancement:
Polymer special lubricants also contribute to improving the surface quality of WPC materials. By reducing friction and improving the flow properties of the composite, lubricants help to minimize surface defects such as melt fracture, streaking, and surface roughness. This results in a smoother and more aesthetically pleasing surface finish, making WPC materials more visually appealing and suitable for a wide range of applications.
Compatibility and Environmental Considerations:
Polymer special lubricants are designed to be highly compatible with both the wood fibers and polymer matrices commonly used in WPC formulations. They exhibit excellent thermal stability, ensuring consistent performance even at elevated processing temperatures. Additionally, lubricants formulated with environmentally friendly additives offer a sustainable solution for WPC production, meeting the increasing demand for eco-friendly materials.
Conclusion:
The application of polymer special lubricants in WPC materials brings numerous advantages, ranging from enhanced processability and improved mechanical properties to superior surface quality. By effectively reducing friction and improving the dispersion of wood fibers within the polymer matrix, lubricants optimize the performance and durability of WPC composites. As the demand for sustainable materials continues to grow, the integration of lubricants tailored for WPC offers an innovative solution for achieving high-quality, eco-friendly wood plastic composite materials across various industries.